فهرست مطالب
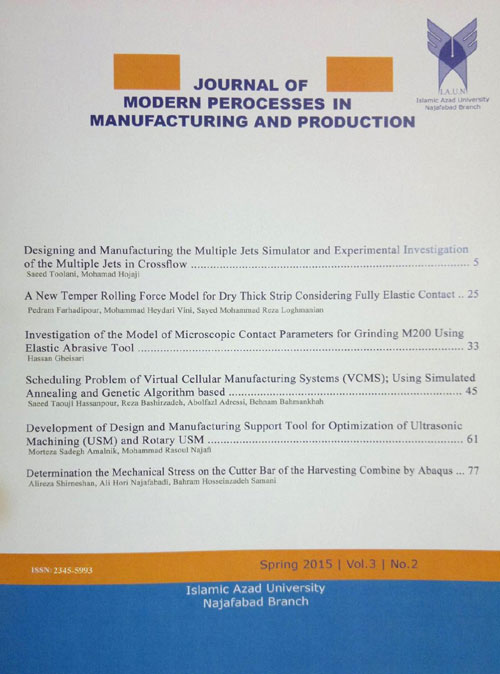
Journal of Modern Processes in Manufacturing and Production
Volume:9 Issue: 2, Spring 2020
- تاریخ انتشار: 1399/04/23
- تعداد عناوین: 6
-
-
Pages 5-22Advances in the additive manufacturing technology have led to the production of complex microstructures with unprecedented accuracy and due todesigning an effective implant is a major scientific challenge in bone tissue regeneration and bone growth. In this research, titanium alloy cylindrical scaffolds with three-dimensional architectures have been simulated and compared for curing partial bone deficiencies. The cylindrical networks in the scaffold (outer diameter 15 and length 30 millimeters) were designed in 36 different convergent, two-layer and three-layer types with 50% and 70% porosity. In all the samples, outer layers were denser than the inner layers. Mechanical characteristics of these scaffolds have been determined by simulating uniform compression load. The stress-strain curve of the samples showed that Young’s modulus and yield stress in the scaffolds with constant porosity were related to a unit-cell and the two-layer scaffolds, without changing Young’s modulus, had higher yield stress. This advantage was more significant in high-density scaffolds.Keywords: Bone Scaffold, Implant, Additive Manufacturing, numerical analysis
-
Pages 23-30In this paper, an innovated method is used for cooling Milling zone of Stainless Steel via Adaptive Neuro-Fuzzy Inference System (ANFIS) using non-touch laser thermometer for non-touch measuring of the temperature. This method is economically appropriate because of its optimization in using coolant. In comparison to the ways which were designed to optimize the ratio of coolant, this method is the best due to its intelligent, fast and trained system via ANFIS .In this method, not only the designing of the ANFIS and using the non-touch laser thermometer makes the cooling process fast but also the accuracy of the system is improved in comparison to the previous designs according to the results in different statistics criteria including MSE, NMSE, R2 and MAPE, which were calculated.Keywords: Milling of Stainless Steel, cooling system, ANFIS, Optimization
-
Pages 31-42
The ball milling of powders is a non-equilibrium technique (similar to rapid solidification processes) that can be used for production and structural modification of materials. Carbon nanotubes (CNTs) are relatively new materials with excellent combination of properties. They are one of the advanced reinforcement materials for engineering composites. Besides the polymer and ceramic matrices, interests are growing recently on the metallic matrices such as aluminum alloys for potential structural applications. Mechanical alloying (MA) is one of the best processing methods for synthetizing Al/CNTs nanocomposites, which results in the uniform dispersion of the reinforcement, inhibits the formation of undesired phases, and produces a nanostructured microstructure. It is of great importance to understand the mechanical alloying of Al/CNTs powder mixture for preparing nanocomposites. As a result, the current short review deals with the basics of theMA process, preparation of nanocomposites by MA, and summarizing the current knowledge on Al/CNTs nanocomposites processed by MA.
Keywords: nanocomposites, Carbon nanotubes, mechanical alloying -
Pages 43-56
This study aimed to investigate the effect of electrical potential on the morphology of Polyvinyl Alcohol/Sodium Alginate electrospun nanofibers, containing herbal extracts of Calendula Officinalis. For this purpose, Poly Vinyl Alcohol (PVA)/ Sodium Alginate (SAlg) nanofibers were prepared using the electrospinning method in aqueous solutions with PVA (8% w / v)/SAlg (2% w / v) blended system in a volume ratio of 80/20. Then Calendula officinalis extract (10% w / v)in a volume ratio of 10% of PVA/SAlg blended system added. Applying potentials were 5, 10, 15, and 20 kV. The electrospun fibers were characterized by scanning electron microscopy (SEM). The results show that all the produced mats had high-porosity and high-surface to volume ratio of electrospun fibers. In all applied potentials, the diameter of the nanofibers containing Calendula was more than the Calendula-free Nanofibers. On the other hand, the diameters of the Nanofibers in each sample decreased with enhancing the potential. Without significant changes in mat morphology, PVA/SAlg electrospun nanofibers diameter including the Calendula could be controlled with electrical potential in electrospinning. The results could be used in antibacterial meshes, wound dressings, drug delivery, and tissue engineering applications.
Keywords: Calendula officinalis, Electrospinning, Nanofibers, Polyvinyl Alcohol, Sodium alginate -
Pages 57-71In this paper, the vibration behavior of the sandwich beams with functionally graded face-sheets is investigated based on the high order sandwich beam theory.The properties of the FGM are varied gradually across the thickness of the structures in accordant with the power-law rule. First-order shear deformation theory and polynomial patterns are used to model the displacements of the face-sheets and the core, respectively. The governing equations of the motion are obtained based on Hamilton’s energy principle and solved by a Galerkin method. An algebraic method is used to reduce the number of equations. Boundary conditions are considered as simply supported and clamped.The effect of the power-law index and geometrical variations are surveyed on the fundamental frequency parameter for different sandwich beams in some numerical examples. In order to verify the results of the present study, they are compared with special cases of the literature.Keywords: Sandwich beam, FGM, High order sandwich beam theory, Vibration, Galerkin
-
Pages 73-84
Hardox-400 with an extra-high yield strength of ~1000 MPa and excellent abrasion resistance is a good candidate for several industrial applications including automotive parts, working tools, barges, loaders, etc. Due to high dimensional precision and to avoid mechanical abrasion of the work-piece, electrical discharge machining (EDM) is a proper machining technique for such steel. The influences of important process parameters, i.e. discharge current and spark pulse cycle on the electrode wear, material removal, surface roughness, and integrity of the machined material is investigated. It was observed in this work that as the discharge current increased, the electrode wear also increased but this occurred with a gradually decreasing rate. On the other hand, increasing the ratio of pulse-on to pulse-off time decreased material removal. Furthermore, it was observed that increasing both the discharge current and the pulse-on time led to a thicker solidified so-called white layer which is more susceptible to cracking and thus is detrimental to the material integrity.
Keywords: Hardox, Discharge Machining, Roughness, Surface Integrity, Pulse Time